Aquí podrás aprender a dibujar el Mapa de flujo de valor (VSM) paso a paso, calculando en cada momento los indicadores que ayudarán a realizar el análisis posterior del estado de la cadena de valor.
Recordemos antes de nada que el mapa de la cadena de valor es una herramienta de mejora continua, del Lean manufacturing, que permite visualizar todas las actividades que se llevan a cabo a lo largo de un flujo de valor de un producto o familia de productos.
El mapa de flujo de valor representa por una parte el flujo de materiales desde lo que es el proveedor hasta el cliente, y por otra, el flujo de información necesario para que el proceso se ponga en marcha. Incluye además, indicadores clave que facilitarán el análisis de la situación actual.
El dibujo del mapa de valor VSM se realiza una vez finalizado el paseo de la cadena de valor y se debe realizar en un sitio tranquilo. Se dibuja siempre a mano, por lo que será necesario disponer de papel continuo grande para ir plasmando en el toda la información recogida.
Pero bueno, la cuestión que nos ocupa ahora es el conocer por dónde empezamos a dibujar y a plasmar toda esta información que se supone que hemos recogido en la etapa del paseo por planta siguiendo el flujo de valor.
Contents [hide]
- 1 Cómo dibujar un VSM (Mapa de flujo de valor)
- 1.1 Primer paso: Calcular el tack time
- 1.2 Segundo paso: Colocar los procesos
- 1.3 Tercer paso: Añadir la información de los procesos
- 1.4 Cuarto paso: Añadir los stocks
- 1.5 Quinto paso: Incluir clientes, proveedores y frecuencias de envío.
- 1.6 Sexto paso: Añadir el flujo de información
- 1.7 Séptimo paso: Añadir flujo de material
- 1.8 Octavo paso: Cálculo del lead time
- 1.9 Noveno paso: Crítica
Cómo dibujar un VSM (Mapa de flujo de valor)
Si recordamos que uno de los objetivos de la utilización de esta herramienta es adaptar la cadena de valor a las necesidades del cliente nos daremos cuenta de que el proceso de dibujado debe empezar en el cliente, lo que ayudará a no perder el enfoque del análisis desde el principio.
Primer paso: Calcular el tack time
Por lo tanto, el primer paso es conocer la demanda del cliente en un periodo de tiempo concreto. Para una demanda de cliente de 18004 piezas al mes, suponiendo 20 días de trabajo al mes, estamos hablando de una demanda diaria de 920 piezas al día.
Si nuestro objetivo es adaptar la cadena de valor a esta demanda el primer análisis que tenemos que realizar a partir de esta demanda es determinar a qué ritmo debe ir la cadena de valor, o lo que es lo mismo: ¿Cada cuánto tiempo debería salir una unidad para poder satisfacer esta demanda? Eso es lo que se conoce como tack time.
Para calcular el takt time, además de conocer la demanda del cliente debemos saber el tiempo por periodo que la cadena de producción está disponible. Por ejemplo, si en un día de trabajo se trabajan dos turnos de 8 horas con dos descansos de 10 minutos por turno, el tiempo disponible por día para poder fabricar las piezas es de: 16 horas de los dos turnos menos 40 minutos de los cuatro descansos. Es decir 920 minutos disponibles que he pasado a segundos suponen 55002 segundos.
Si tenemos que fabricar 900 piezas, qué es lo que pide el cliente, en 55200 segundos, el ritmo de producción , el tack time, debería ser de 60 segundos por pieza es decir deberíamos ser capaces de sacar una pieza cada 60 segundos para poder satisfacer la demanda del cliente.
Segundo paso: Colocar los procesos
Seguiremos nuestra representación del mapa de valor colocando los procesos. Un proceso es aquel por dónde fluye el material y la información y está desconectado del proceso siguiente. Es decir, siempre que haya inventario en espera en medio, que ambos procesos tengan programación independiente y que trabajen en Bach.
Los procesos se dibujarán de izquierda a derecha siguiendo el orden de secuencia de fabricación sin tener en cuenta la forma en como están ubicados físicamente los procesos en el Lay out.
Tercer paso: Añadir la información de los procesos
Nuestro tercer paso será añadir las casillas de información de cada proceso. El principal problema que nos vamos a encontrar las empresas la falta de datos que permitan el cálculo de indicadores, por lo que habrá que hacer un pequeño esfuerzo para, al menos, poder disponer de la información básica que nos permita calcular al menos estos indicadores que son los genéricos.
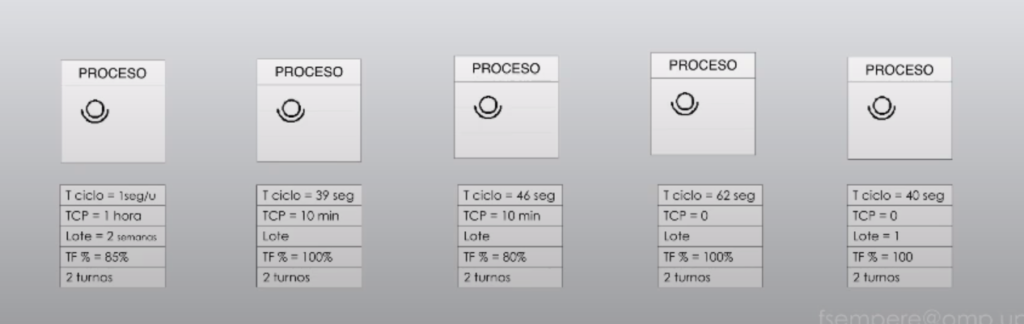
Empecemos por el tiempo de ciclo que es el tiempo que pasa entre la salida de una pieza y la siguiente y mira por lo tanto lo que es el ritmo de producción de un proceso y se calcula dividiendo el tiempo disponible por periodo por la cantidad producida en ese mismo periodo.
Si tenemos un tiempo disponible diario de 55200 segundos, que es lo que has visto antes y en ese tiempo hemos producido 1200 piezas el tiempo de ciclo será de 46 segundos por pieza.
El lote de fabricación se podrá expresar tanto en unidades como en tiempo. Por ejemplo, un lote para para 3 días.
El tiempo de cambio de partida es el tiempo que se tarda en pasar de un lote a otro, en cambiar de un tipo de producto a otro en una máquina o equipo concreto.
Se indicaran también los operarios necesarios en cada proceso y el tiempo disponible para cada proceso. Es bastante habitual en las empresas que no todos los equipos trabajen las mismas horas o los mismos turnos porque las líneas suelen no estar balanceadas.
Tiempo de funcionamiento (Tf): Otro dato muy importante cuando trabajamos con máquinas es conocer el porcentaje de tiempo que la máquina está funcionando lo ideal sería poder calcular el OEE pero si no tenemos suficientes datos para calcular este indicador al menos deberemos tener una idea del tiempo de funcionamiento de la máquina expresado en porcentaje.
Una vez tengamos este por su porcentaje de funcionamiento si lo multiplicamos por el tiempo disponible y lo dividimos por el tiempo de ciclo obtendremos la capacidad productiva de cada proceso en piezas hora.
Cuarto paso: Añadir los stocks
El paso 4 es identificar los puntos donde se acumula el inventario tanto de materia prima, como de producto final y semielaborados. El icono que se utiliza es el triángulo y debe ir acompañado del número de unidades de stock en cada caso.
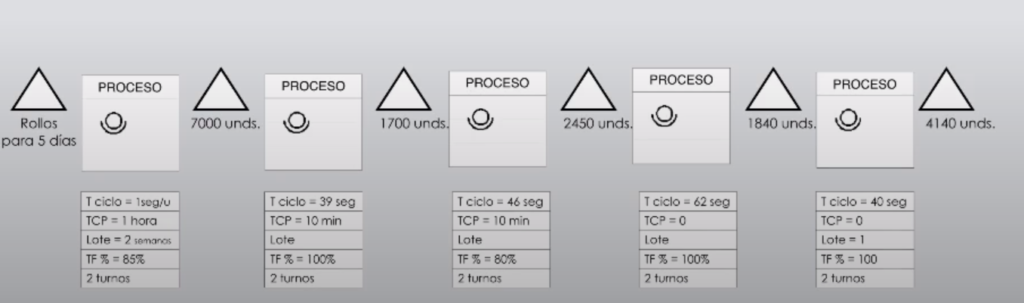
No dibujaremos todas las materias primas sino que nos centraremos solo en aquellas más importantes.
Quinto paso: Incluir clientes, proveedores y frecuencias de envío.
Pasamos ahora indicar cómo se realizan los despachos a nuestros clientes y con qué frecuencia. En nuestro ejemplo, es a través de camiones propios con una frecuencia diaria.
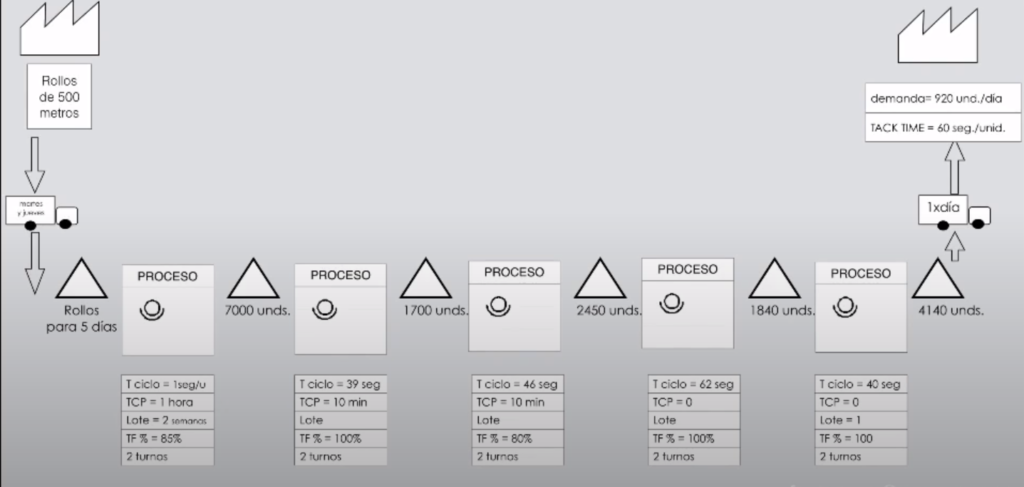
Si nos centramos ahora en el proveedor tenemos también que definir las características de despacho de nuestros proveedores en cantidad, frecuencia y modo.
El proveedor de nuestro ejemplo nos se entrega la materia prima en rollos de 500 metros y en camiones que vienen los martes y los jueves.
Sexto paso: Añadir el flujo de información
El siguiente paso es el de añadir el flujo de información que se representa por una línea fina que irá en zig-zag cuando sea por conductos electrónicos en lugar de papel.
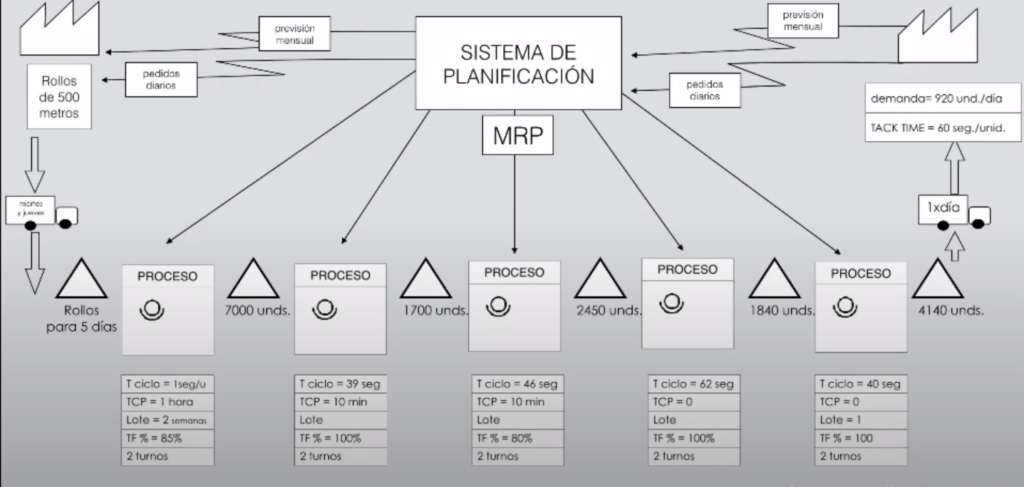
Se utiliza una casilla pequeña para etiquetar o describir la información que se colocará encima de esa misma línea. Se dibuja de derecha izquierda, en la mitad superior del espacio del mapa y el departamento de control se dibuja con una casilla de proceso.
Séptimo paso: Añadir flujo de material
Ese momento de añadir el flujo de material que pueda votar dos formas principales:
Flujo push
Se produce cuando cada proceso tiene su programación y fabricar bloques distintos atendiendo a lo que conviene por motivos de eficiencia de proceso.
En este caso los procesos fabrican piezas y las envía no empujan hacia el proceso siguiente sin tener en cuenta las necesidades del siguiente proceso. Este flujo se representa con una flecha a gruesa negra.
Flujo pull
Se produce cuando la programación de producción la determina el cliente a través de tarjetas Kanban, entendiendo como cliente de un proceso la etapa que va detrás se representa con una flecha circular.
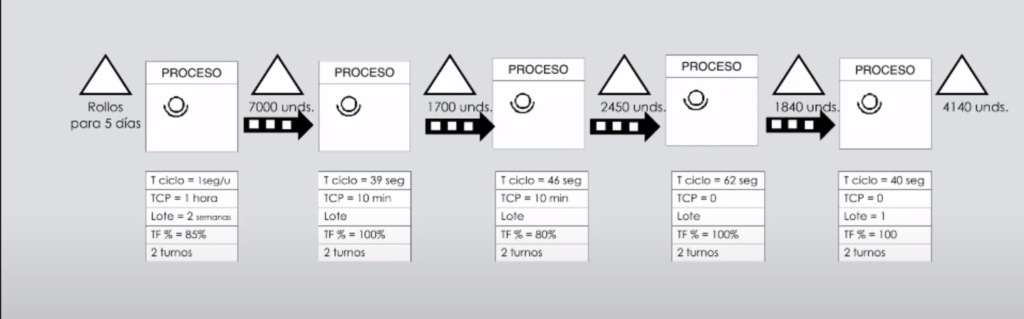
Octavo paso: Cálculo del lead time
Para finalizar sea línea de tiempo que nos ayuda estimar el lead time, que es el tiempo que necesita una pieza en recorrer el taller de un extremo a otro desde la llegada de la materia prima hasta el despacho del cliente.
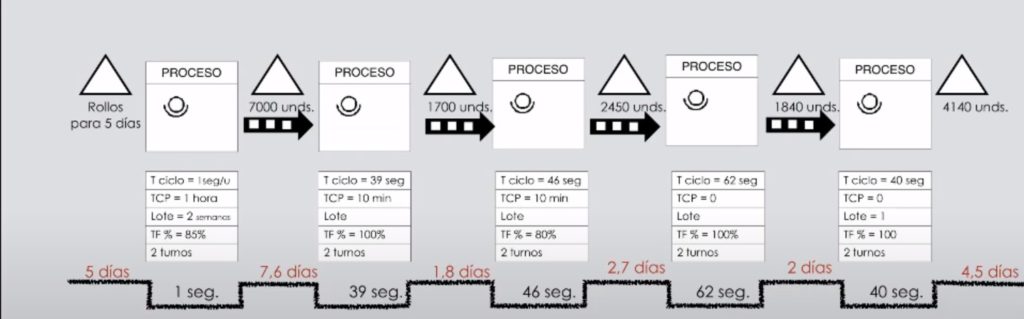
El lead time estará formado básicamente por la suma del tiempo que tarda una pieza en ser procesada a partir de lo que es el tiempo de ciclo de cada proceso y el tiempo de espera de una pieza en las áreas de inventario.
La línea de tiempo se dibuja debajo de las casillas de proceso y los triángulos de inventario separando tiempos correspondientes actividades de valor añadido, del de actividades de no valor añadido.
Se trata de una línea quebrada en la que las actividades de valor añadido se ponen en los valles y las de no valor añadido se pone en las crestas.
Los tiempos de los procesos se corresponden con los tiempos de ciclo y generalmente se trata de actividades que generan valor al contrario que los inventarios que son actividades que no generan valor.
El tiempo de espera en inventario se calcula dividiendo las unidades de inventario por la demanda diaria sumando todos los tiempos de la línea de tiempo obtendremos una estimación del lead time, que para nuestro ejemplo asciende a poco más de 23,6 días de los cuales solo 3,13 minutos se corresponde con actividades que generan valor lo que supone un ratio de valor añadido muy muy bajo.
Noveno paso: Crítica
Una vez dibujado el mapa de cadena de valor se pasará a la siguiente etapa en la que se analizará la situación actual rediseñando la cadena si se considera adecuado.